Kautschuk - der Rohstoff
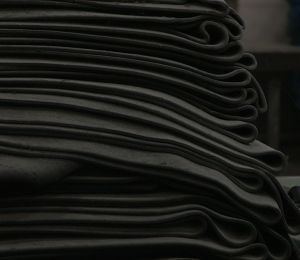
Woher stammt der Rohstoff geographisch? Die Herkunft von Naturkautschuk ist gut überschaubar. Die fünf wichtigsten Produzentenstaaten von Naturkautschuk sind heute Thailand, Indonesien, Malaysia, Indien und die Volksrepublik China. Die größten afrikanischen Produzenten sind die Elfenbeinküste, Nigeria und Liberia. Die Weltproduktion belief sich 2003 auf 7,6 Mio. t (Trockengewicht), wovon 80 % exportiert wurden. Hauptabnehmer sind die USA, Japan, China, Deutschland und Frankreich.
Und welche Unternehmen bieten den Rohstoff an? Die größten Kautschukverarbeiter in Europa sind ein kürzlich ins Leben gerufenes Joint Venture von Lanxess und Saudi Aramco, ein ebensolches Joint Venture von Sinopec und Mitsui sowie Dow Chemical und Sabic. Diese Verarbeiter beliefern dann die sogenannten Compounder, von denen wir unseren Kautschuk beziehen.
Die Compounder fügen verschiedene Materialien hinzu wie Füllstoffe, Weichmacher, Verarbeitungshilfsmittel und Haftvermittler sowie Farbstoffe und Pigmente als weitere Zusatzstoffe. Der Kautschuk wird also, je nach geplanter Verwendung, durch Materialien ergänzt. All die genannten Stoffe haben unterschiedliche, verarbeitungsfördernde und qualitätserhöhende Funktionen. So dienen beispielsweise die Verarbeitungshilfsmittel und Haftvermittler als Abbaumittel (Mastikationsmittel für Kautschuke), Dispergierhilfe, als Gleitmittel für glatte Extrusion und Kalandrierung; zu ihnen zählen auch Harze als Klebrigmacher (Konfektionshilfe) und Haftvermittler für Metall-Elastomere. Farbstoffe etwa dienen als Stabilisatoren und Alterungsschutzmittel, die Wärme stabilisieren und als Schutzmittel gegen Licht fungieren. Pigmente ermöglichen verschiedene Farbtöne und gewährleisten Licht- und Wetterechtheit sowie Wärmebeständigkeit.
Ziel des Aufbereitungs- und Veredlungsprozesses dieser Unternehmen ist es, bewusst eine Optimierung der Eigenschaftenprofile des Rohstoffes vorzunehmen. So ist gewährleistet, dass wir im Produktionsprozess die besten Inhaltsstoffen verwenden.
Kautschuk – Das Beste aus Natur und Synthetik
Neben Naturkautschuk verwenden wir auch sogenannten „synthetische Kautschuksorten“ – je nach Verwendungs- und Einsatzzweck des Produktes.
Eine Übersicht der verschiedenen Kautschukarten finden Sie hier. Dort nennen wir neben den Kurz- und chemischen Bezeichnungen auch Handelsnamen, Eigenschaften und übliche Anwendungen. So gewinnen Sie einen schnellen Überblick über die Vielfalt und mögliche Einsatzorte.
Naturkautschuk
Der Naturkautschuk, gewonnen aus dem Kautschukbaum in Form von Kautschukmilch (Latex genannt), stellt eine wässrige Suspension mit kompliziertem Aufbau dar. Die antiken Mesoamerikaner kannten das Verfahren der Vulkanisation nicht. Sie erreichten aber durch Zugabe von Baum- und Pflanzensäften die Umwandlung des plastischen Latex zu einem elastischen, gummiartigen Material. Im Jahre 1839 erfand Charles Goodyear das Verfahren der Vulkanisation, durch das der plastische Kautschuk in elastisches Gummi umgewandelt werden kann.
Betrachtet man die Vielzahl hochwertiger Naturkautschukprodukte wie z. B. Scheibenwischer, Brückenlager, Schienenpolster und Handschuhe, so ist Naturkautschuk ein echtes Verkaufsargument. Aufgrund dieser Tatsache wird Naturkautschuk für die Herstellung von Antivibrationselementen eingesetzt.
Wir setzen Naturkautschuk dann ein, wenn nur aus diesem Rohstoff die besten Produkte hergestellt werden können.
Synthetischer Kautschuk
Gegenwärtig beträgt der Anteil des synthetischen Kautschuks am Gesamtbedarf von Kautschuk etwa 60 %. 1998 lag nach Angaben des International Institute for Synthetic Rubber Producers (IISRP) der Umsatz bei 10,4 Millionen Tonnen, wovon 70 % in die Automobilindustrie gingen. Die umsatzstärksten synthetischen Sorten sind: Styrol-Butadien-Kautschuk (SBR), Polybutadien Kautschuk (BR), Nitrilkautschuk (NBR), Chloropren-Kautschuk (CR) und Ethylen-Propylen-Dien-Kautschuk (EPDM). Für die Teppichindustrie bedeutsam ist Styrol-Butadien-Latex (SBL) und für Anwendungen bei Temperaturen bis zu 300 °C Silikonkautschuk (SI).
Erdölausgangsprodukte sind oftmals die Basis der Synthesekautschuke. Die Einsatzgebiete für diese Kautschukart sind vor allem Produkte, an die extreme Ansprüche bezüglich chemischer Beständigkeit, tiefes und hohes Temperaturverhalten oder Oxidation bei Witterung gestellt werden. Deshalb ist es oftmals unumgänglich, auf einen geeigneten Synthesekautschuk überzugehen.
Eigenschaft und Qualitätsmerkmal: Die Härte von Kautschuken
Die Härte von Kautschuk wird nach DIN 53 505 gemessen. Bei diesem Verfahren wird der Widerstand gegen das Eindringen eines Kegels gemessen. Die Einheit der Härte wird grundsätzlich in SHORE ausgedrückt.
Die Shore-Härte, 1915 von dem US-Amerikaner Albert Shore entwickelt, ist ein Werkstoffkennwert für Elastomere und Kunststoffe und ist in den Normen DIN EN ISO 868 und DIN ISO 7619-1 festgelegt. Bei der Bestimmung der Shore-Härte spielt die Temperatur eine höhere Rolle als bei der Härtebestimmung metallischer Werkstoffe. Deshalb wird hier die Solltemperatur von 23 °C auf das Temperaturintervall von ± 2 K beschränkt. Die Materialdicke sollte mindestens 6 Millimeter betragen
Shore-A wird bei Weich-Elastomeren nach Messung mit einer Nadel mit abgestumpfter Spitze angegeben. Die Stirnfläche des Kegelstumpfs hat einen Durchmesser von 0,79 Millimetern, der Öffnungswinkel beträgt 35°. Auflagegewicht: 1 kg, Haltezeit: 15 s. Es werden Shore A und Shore D unterschieden. Handmessgeräte müssen meist sofort beim Aufdrücken auf die Probe abgelesen werden, der angezeigte Wert nimmt bei längerer Haltezeit ab.
Shore A
- 100 – 92: sehr hart
- 90 – 80: hart
- 78- 68: mittelhart
- 66 – 52: mittelweich
- 50 – 40: weich
- 38 – 28: sehr weich
Shore-D wird angegeben bei Zäh-Elastomeren nach Messung mit einer Nadel, die mit einem 30°-Winkel zuläuft und eine kugelförmige Spitze mit einem Durchmesser von 0,2 Millimetern hat. Auflagegewicht: 5 kg, Haltezeit: 15 s